








Automated production line for glass fiber continuous winding pipes
It consists of a spindle transmission device, an overall frame, a steel belt propulsion device, an aluminum beam fixing plate, a steel belt circulation head, a steel belt circulation lead-out head, a steel belt supporting aluminum beam, a steel belt
CFW series continuous pipe winding machine introduction
Continuous pipe winding machine equipment function, composition and principle:
Equipment function:
CFW continuous pipe winding machine is the main equipment on the continuous pipe production line, used for continuous winding pipe production.
Equipment composition:
It consists of a spindle transmission device, an overall frame, a steel belt propulsion device, an aluminum beam fixing plate, a steel belt circulation head, a steel belt circulation lead-out head, a steel belt supporting aluminum beam, a steel belt, an inner lining layer cutting yarn device, a structural layer cutting yarn device, a sand adding device, an inner lining layer cutting yarn rack, a structural layer cutting yarn rack, a structural layer winding yarn rack, an inner lining layer resin stirring and pouring device, a structural layer resin stirring and pouring device, an infrared heating system, a polyester film winding rack, a surface felt winding rack, an outer protective layer winding rack, an inner lining layer pneumatic pressure roller, a structural layer pneumatic pressure roller, a finishing pneumatic pressure roller, a hydraulic lifting platform, an online cutting, trimming device and a dust collecting device, a PLC control system and an electrical control system.
Working principle:
The mold consisting of an aluminum beam, an aluminum beam fixed disk, a steel belt circulation lead-out head, a steel belt circulation head, and a closed-loop steel belt is installed on the main transmission device of the winding machine. When the main transmission device of the winding machine drives the mold to rotate, the steel belt will be wound on the aluminum beam evenly distributed along the aluminum beam fixed disk. At the same time, under the action of the steel belt pushing device, the steel belt moves axially along the winding main shaft. The steel belt pushing device pushes the steel belt axially by one steel belt width for each rotation of the main shaft. When the steel belt is pushed to the tail of the aluminum beam in the axial direction, the steel belt enters the steel belt circulation lead-out head and the steel belt circulation head, and the steel belt is introduced into the main shaft (hollow shaft) of the main transmission device of the winding machine, and returns to the starting point of the winding through the steel belt winding guide device. In this way, the steel belt forms a winding, pushing, leading-out, leading-in, and rewinding cycle. When the steel belt forms a winding cycle, a layer of polyester film and surface felt is wound on the steel belt. At the same time, the lining glue spraying device and the structural layer glue spraying device above spray an appropriate amount of resin on the steel belt. The lining layer cutting yarn device and the structural layer cutting yarn device sprinkle an appropriate amount of chopped fibers on the steel belt. The sand adding device sprinkles an appropriate amount of quartz sand on the steel belt, and the winding yarn frame provides hoop-wound fiber yarn. When the hoop-wound fibers, chopped fibers, resin, and quartz sand on the steel belt are fully mixed and soaked under the action of the rolling device. Under the action of the steel belt, it moves along the main shaft axis, enters the infrared heating zone, heats and solidifies, and continues to move along the main shaft axis and leaves the steel belt mold. The hydraulic lifting platform rises in sequence, and the rollers on the platform hold up the solidified pipe. After the pipeline has a certain length, the online cutting and trimming device starts to cut and trim the pipeline. In this way, the pipeline production is completed. The amount of lining cutting yarn, structural layer cutting yarn, winding yarn, quartz sand, and resin are pre-set and controlled by PLC. The resin temperature and quartz sand temperature are also controlled by PLC.
WHY CHOOSE US ?

STRENGTH
The group currently has a standard factory area of over 20000 square meters and an annual production capacity of around 100 sets of pipeline equipment

INNOVATION
Since its establishment, the company has continuously carried out technological innovation and industrial upgrading, and has been rated as a national high-tech enterprise

SERVICE ASSURANCE
Our company always focuses on customers and strives to improve product quality and service level, with the goal of zero product defects and zero customer complaints

PARTNERS
Our success cannot be achieved without the strong support of every partner
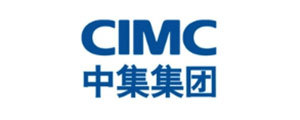
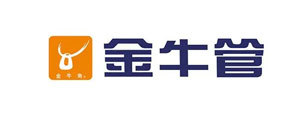
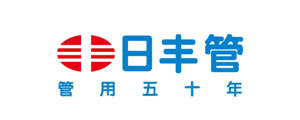
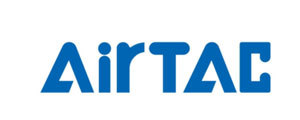
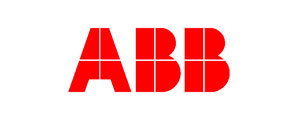
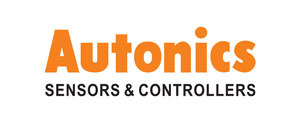
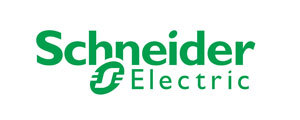
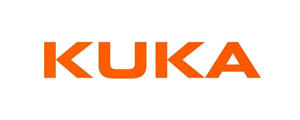
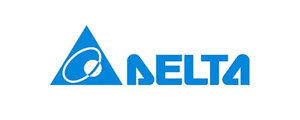
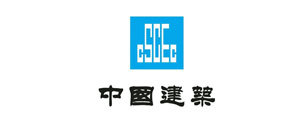
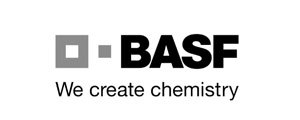
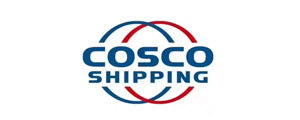

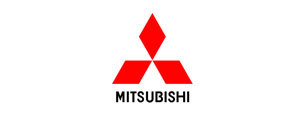
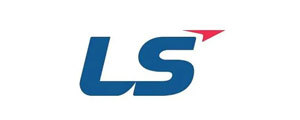
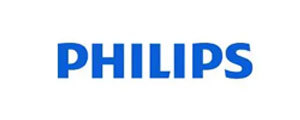
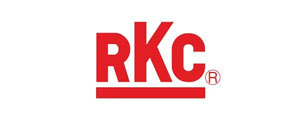
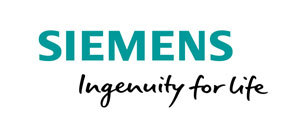

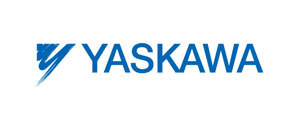

Inquire
Note: Please complete this form, and we will contact you by the next business day.